Emulative Emergence - Mechanism
From the complete failure of a Pop-Up Windows mechanism I attempted and from dealing with Maker Faire- this concept of securing motor shafts is - though difficult with the tools available here at ITP - would be a challenge even with the best and widest range of work tools.
For the Pop-Up failed mechanism- I attempted to make four gears align and the motor shafts created quite a problem for me, when it came to precise mounting... granted these were done in a super quick and almost certain doomed to fail from the beginning because of time constraints, (i'm ok, but merely listing issues that came to the fore this past week)-
While in the midst of this problem- Kina Smith got me on the metal lathe.
I am often faced with attempting to mount round rotating things to other round things and have the round rotating things push/propel/pull etc. the other round thing it fits into.
This is problematic and when I am faced, again and again, with a problem, my way to deal with these are to systemize the solution.
Therefore, I will be running on the lathe, my own custom bushings with keyways on a mill etc.
---http://en.wikipedia.org/wiki/Key_(engineering)
---
---http://www.mcmaster.com/#machine-keys/=r1pjxu
---
I am so so tired of cobbling together what should be precise.
Here's an image of kind of what I am thinking about. I need to put in some keyways... This design is not anything new, but instead of having to work around pre-fabbed stuff, I can make my own and in addition, I can extend any of these to match whatever needs may arise in the fabrication process. Therefore- Why the hell not?! (yaaay!)
I ordered some machinable aluminum tube from Online Metals - Four 1ft length of 3/4" stock.
Here's the image of what I ran on the lathe last week:
This side is bored and threaded for 1/2" bolt
the opposite side threaded for a 5/16"
The widest part of the tube is stock, whereas the smaller part has been reduced to be fit inside the metal frame... i.e. WOW!
I am so tired of the cobble. While I design the rubber, I am thinking of my next steps in regards to robust long-term installs of kinetic work.
Here is a quick mock up of what I will be working on:
I started with this:
Then I made some threads etc:
So, I still had in mind the crank/piston. However, I was reluctant to test much of anything until I was sure what my material would be.
Now that I have a solid cast of the rubber node, I can now prepare for the kinetic work.
The crank from the previous post was too large and heavy to for the motor to complete a full rotation.
So I rebuilt the prototype to accommodate a horizontal and paired down system.
I got it moving - a 12" long arm- as the longer the stepper shaft is from the point of rotation- the more linear motion I achieve.
However, even the slightest amount of friction or weight, at that length, the motor would stall. Therefore, if I want to give a large distance of push and pull, I need to redesign my kinetic structure completely.
To the Rack and Pinion:
So I did a diddy on Rhino:
In the mock up for the horizontal crank thing, I got a lazy susan to help support the arm (so that the motor would only have to spin the arm and not have to concern itself with lifting it as well- though it did little to help).
Well, that long telescoping thing is a drawer slide meant to behave like the lazy susan for this mock-up. This is the one in the mail:
I wanted to design around this part, so I remodeled it in Rhino
The rack aspect of the design is living on the drawer slide:
I am placing ball bearings on the non-telescoping base of the drawer slide. I bought some ball-bearings to mount there
I am still really anxious about how much these steppers can take.
I need to design something lightweight- as the length is so great.
Mcmaster is awesome-
http://www.mcmaster.com/#rack-and-pinion-gears/=r43iza
--- they are a bit small....
So I did some research- and found a motor which has 262 oz. per inch of holding torque.
I am faced with either having multiple steppers for linear motion per node, or one.
This particular stepper runs approx. 86$. shipping from Anaheim California (not overseas).
Model + 23Y202S-LW8....
So Remade the Rhino file to represent the McMaster Rack and Pinion- kind of- and the new Stepper Motor- kind of-
This is that bracket, mounted with ball bearings ....
This is the rack I got from McMaster upside down. I mounted it with these cut outs onto the plexi:
This is the plexi to hold the rack in place, gluing the plexi bits from the above image onto the housing....
This is how it lives in the housing...
I made bottom slots to ride on the ball bearings...It runs smoothly.
I am still a bit concerned over the weight of the rubber and am considering casting it at half thickness:
However, at half thickness, the structural integrity might be compromised...
In anticipation of the motor's arrival, I re-made the H-Bridge circuit with more robust wires and ready for a heat sink, as the motor will draw a crap-load of amperage and will get hot. It is a SN754410...
I went home and started thinking about how to skin the rubber cast -
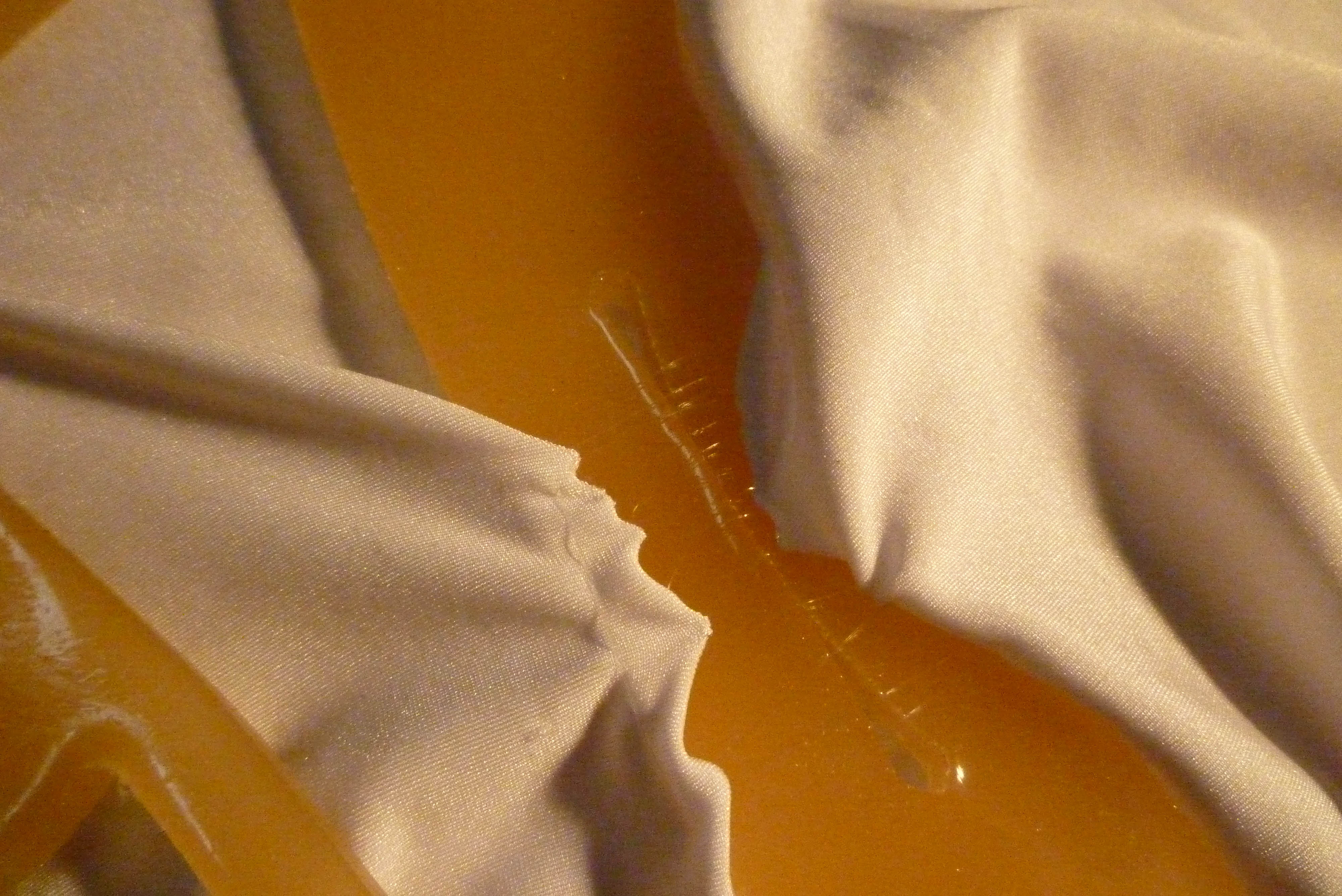
I don't like this exactly, but there is something there. Were I to skin this taught, it would collapse on itself. However, I need to know how the motor will push and pull the rubber to know how to skin it.
So I got my beefy stepper, the circuit working, however, the lathe is not centering properly, so I am unable to steadily mount the spur gear to the motor shaft. Regardless, I wanted to make sure it could handle the system I have built in with no problems. I finished making the rack and attached the far end to the bottom most extendable end of the shelving bracket. Here's a quick test- to assuage my fears of lack of torque:
Apologies for the overblogging- this is how I blog on my own site - so I follow suite here- in kind.
This week has been monumental in movement
I have made the rack successfully prod the rubber with a full extension (not shown here, but does so with out fail).
I have begun the process of upgrading the framework for the kinetic stuff, and have ordered aluminum U-Channels to better house the rack for the rack and pinion, as the current iteration is flimsy and I have a video of the teeth not meeting the gear throughout the entire rack length (because of inconsistent mounting in one area- also not shown)- I built the plexi as a prototype, so, yay!
In addition, through conversation with Ben Light, I have altered my game plan for Horizontal movement (the rack is for "latitude", say), and I am still married to also having longitudinal movement. Initially, I had tried to mount a stepper with a threaded rod drive- the most affordable ones came from sparkfun (i ordered them over break in my stepper research). They worked, kind of:
There were several issues- it only has 21 N.m torque (not enough in my estimation) and its' threadcount/MM size is sort of impossible to find -... the shaft length is but what is above in the video (!) ....therefore, and again with generous assistance from Ben Light, I will make my own screw drive:
Something akin to:
as large C-Clamps are sort of ready-mades, I purchased the largest I could find within a price range - 10" C-Clamps:
I cut them off with an angle grinder like so..
While I am waiting on the motors to power the screw drives - I figured out how to mount the screw to the frame for the node:
I may need to make adjustments to this housing, as they are somewhat offset because of millimeters of lack of space for the butt ends of the c-clamp, but that will lie in how the motors are mounted.
For now, these may work as installed...
I want four per node - one per corner, so that they may tension and loosen the taught-ness of the rubber.
I believe firmly that the diversity of the movement will give me more to compose with concerning behaviors and I am excited at the proposition of coding it!
Here is a sketch of all mechanisms proposed thus far:
I purchased 12 of those gearbox cheap-o but powerful dc motors from MPJA (4 per node, with an anticipation of 3 built) to automate the screw drives. I am certain they have enough torque for this application, as I have used them before and they are super beefy!
I cut the handle off of the c-clamp threaded rod - the hole on the rod for the handle was pretty huge. So I lopped the ends off of each right at "the quick" with an angle grinder. I only had 3/4" machinable rod - the rod - of I made a connection to the motor shaft - would so little wall thickness that it would be not structural. Therefore I machined off some of the threading and turned that end rod to ~.5 thickness:
I then machined some collets for the end of the c-clamp to live within and room to mount the motor shaft on the other-
In addition- I have made the coupler for the massive stepper. I stripped the threading I made inside the collar because of an all too beefy set screw. It works for now. I will make it again with appropriately sized set screws...
I also need to come up with a way to mount a bracket of some size to the end of the U-Channel. So I again went to the lathe (after having tried to mount some bracket I had laying about and having failed at being sloppy)- So I did this diddy -
(will chop the screws to size once)
I also mounted the rack and screwed it in with 2 1/8" plexi strips (to assure that the gear will have appropriate connection)
CIRCUIT
The huge stepper draws approx 1.55 amperage - it burned the H-bridge with just minutes of running.
I queried Rosenthal as to how to drive a stepper with something of a larger current rating: He gifted me with IRF520 MOSFETs. So I read about them a bit, as I assumed that I give current to allow the stepper current to flow and power the stepper:
http://reibot.org/2011/09/06/a-beginners-guide-to-the-mosfet/
This was my initial thought:
Rosenthal sounded an astute negative to this schematic and linked me to several others:
https://forum.sparkfun.com/viewtopic.php?f=20&t=28181
https://www.google.com/search?q=Hexfet+solenoid+circuit&safe=off&client=safari&hl=en&tbm=isch&tbo=u&source=univ&sa=X&ei=c0o0U7yjLfStsQSh1IDQDA&ved=0CCsQsAQ&biw=1280&bih=641
So I selected this schematic:
I spent the large portion of today trying to fig. out why the hell the circuit wasn't working - the bench supply kept asking for amperage even with no load... meaning something was askew with the circuit.
I did the typical troubleshooting by pairing down the complexity of the circuit and what the load would be.
Long story short- Jeff Federsen spent about 1/2 an hour with me - I learned a great deal about MOSFETs, as we got the circuit working (I needed a super beefy resistor to ground) -
He, like Rosenthal, urged me to use an out-of-the-box driver as these have been proven to work. I ordered a Big Easy Stepper Driver from Sparkfun *** I MUST HEAT SINK THE CHIP**
I don't know why I am so stubborn sometimes/
There is a chance that the Big Easy Driver will also not function as intended as the amperage rating really is not the amperage rating... per comments, but the failure rate of this breakout will be much less than my own crafted in ignorance Mosfet circuit.
So, crossed fingers.
The rest of today will be spent preparing the circuit board to house 2 H-Bridges for the DC Screw Drives...
I am working on getting three of these completed so, sometimes as I go, while I remember what it is that I am doing, I do it three times over.
In keeping with that, my most amazing boyfriend - Boris - has graciously agreed to build the other two frames to house the other two nodes.
I have been going back and forth with him with ordering etc. Here is a rough sketch of the diagram.
----
I have been hesitant to take the drawer slide off of its plexi housing, however, in keeping with the idea of making many of these, I wanted to make the mounting more systematic - in addition to how the mounting of the drawer slide it goes in tandem with how the motor with the gear is mounted.
so I tossed the plexi aside and used the aluminum housing-
----
12 DC motors arrived this week!
I test mounted one of the older ones I had to see how it mounted:
To make it flush, I had to drill out a ~3/4" hole in the metal frame- This initial one is pretty rough-
----
In keeping with the arrival of the DC motors, I mounted them to the collets I made earlier (drilled the motor shaft holes the appropriate size
I tapped set screw holes to secure the collet to the D-Shaft of the motor (currently pictured with inaccurate screws/bolts)
I then mounted the DC motor to the frame with some l brackets and 10-32 screws.
I ran into some problems with the planned mounting of the screw part of this actuator.
I thought this might be an issue - meaning- to me it is more important to have the motors mounted with care and supported by the frame - than to have the threaded rod as supported - meaning - It is easier to mount the screw part-
I did this- though it remains to be seen if it is the appropriate step
Then I hooked it up and ran it at 12V:
It is sooooooo slow - I knew this going in - I could have tried other options of motor - but I went with the sure thing. I can work with this, and happily so! Yay!
In addition - I fixed my nasty hole from above and made another sexy hole
with this little fella- so worth the cost!
----
In addition I prepared 4 more c-clamps (four more for all three nodes to be completed). I also remade the shaft coupler for the stepper and spur gear- as I had stripped the metal set screw from the prior iteration, I bored out the spur gears' mounting hole to .5".
This allows for a thicker wall of the aluminum to provide more threads to hold the set screw in place.
I made them a bit too long - meaning I need to trim them shorter to fit within the gear's thickness-
That being said, I had to pressure mount them in the gear=
I came in and trimmed the coupler - drilled and tapped 4-40 holes to connect the gear to the two sides of the coupler:
I also tapped a screw into the flat part of the D shaft of the stepper motor.
It is now affixed properly!
______
mount the motor to the rack
mount the DC to the frame
finish wiring circuit
test momentary switches
I've been working on mounting motors and building the bare bones of a circuit.
This is the mount for the stepper on t!he rack and pinion
It needs to be square.
It is mounted at a precise height to match the rack
I got my big easy stepper driver, soldered it in and had some problems which I should not have had. the circuit kept shutting my computer off, meaning there was a short somewhere, or somehow back current was getting through. It took me many hours to fig. out what was wrong - me and my multimeter, a separate big easy and a regular easy-
I also wired up the H-Bridges and go the DC motors running. However, what I thought I had fixed regarding the big easy, I had not. Similar issues.
(It was a tiny tiny piece of solder connected to +5V from the Arduino that would sometimes connect and sometimes not!)
I got it working though!
In addition- I mounted all four motors to the frame, labeled all the wires, temporarily ran those, and mounted one more screw drive (I am awaiting yet another McMaster order for the L brackets).
I also had these laying around and are perfect for motor response signals and I ordered 12 more (though I think I need almost twice that, so will order 15 more).
To save on Pins, I will wire both direction switches on one Arduino Pin.
and simply tell my motor to stop moving.
I am running out of Pins on my ardunio, so I need to wire the NO switches (on/off- digital) with Digital read off of the Analog pins!!!
http://forum.arduino.cc/index.php?topic=28720.0
In addition I began looking at software serial to hardwire serial across all nodes.
http://arduino.cc/en/Reference/SoftwareSerial
Reading into this- simultaneous serial signals are not allowed. therefore perhaps this library will work?
http://www.pjrc.com/teensy/td_libs_AltSoftSerial.html
In addition it has been difficult keeping track of all of the materials, and of those which I need to complete future nodes (meaning, in my receipts there are materials which did not work while prototyping) therefore I am keeping and somewhat updating useable and ness. actuator kinetic materials. Here is kind of what it looks like and I am only using it to track what I have and have not purchased, and somewhat - status reports. It is sloppier than i would like, but alas, these are trying times! :)